Blog
The Key Steps to Constructing your Electric Depot
The construction phase marks a pivotal moment and a key step in the journey of electrifying your fleet. It is where all the planning and preparation come together, turning a vision into a fully operational and reliable depot once designs have been finalised. The complexity of this stage involves much more than simply installing charging stations, it requires managing the installation of critical infrastructure, ensuring compliance with a range of regulatory standards, and coordinating multiple contractors. The goal is to create a functional, scalable, and future-proof charging ecosystem that will support your fleet’s long-term needs.
At EO, we support every step of the construction process. From managing compliance and safety standards to overseeing infrastructure installation and coordinating preventative maintenance, our team ensures that the project runs smoothly and efficiently. We work alongside trusted contractors to ensure that your depot is delivered on time, within budget, and with futureproofing in mind to meet the evolving need of your fleet.
In this blog, we will provide an overview of the depot construction process, from pre-construction planning to the final handover, highlighting key stages and best practices that ensure a smooth, efficient, and successful build. With effective project management and adherence to industry standards, you can minimise disruptions and set the foundation for future operational success while also ensuring your EV infrastructure is designed to scale alongside your business.
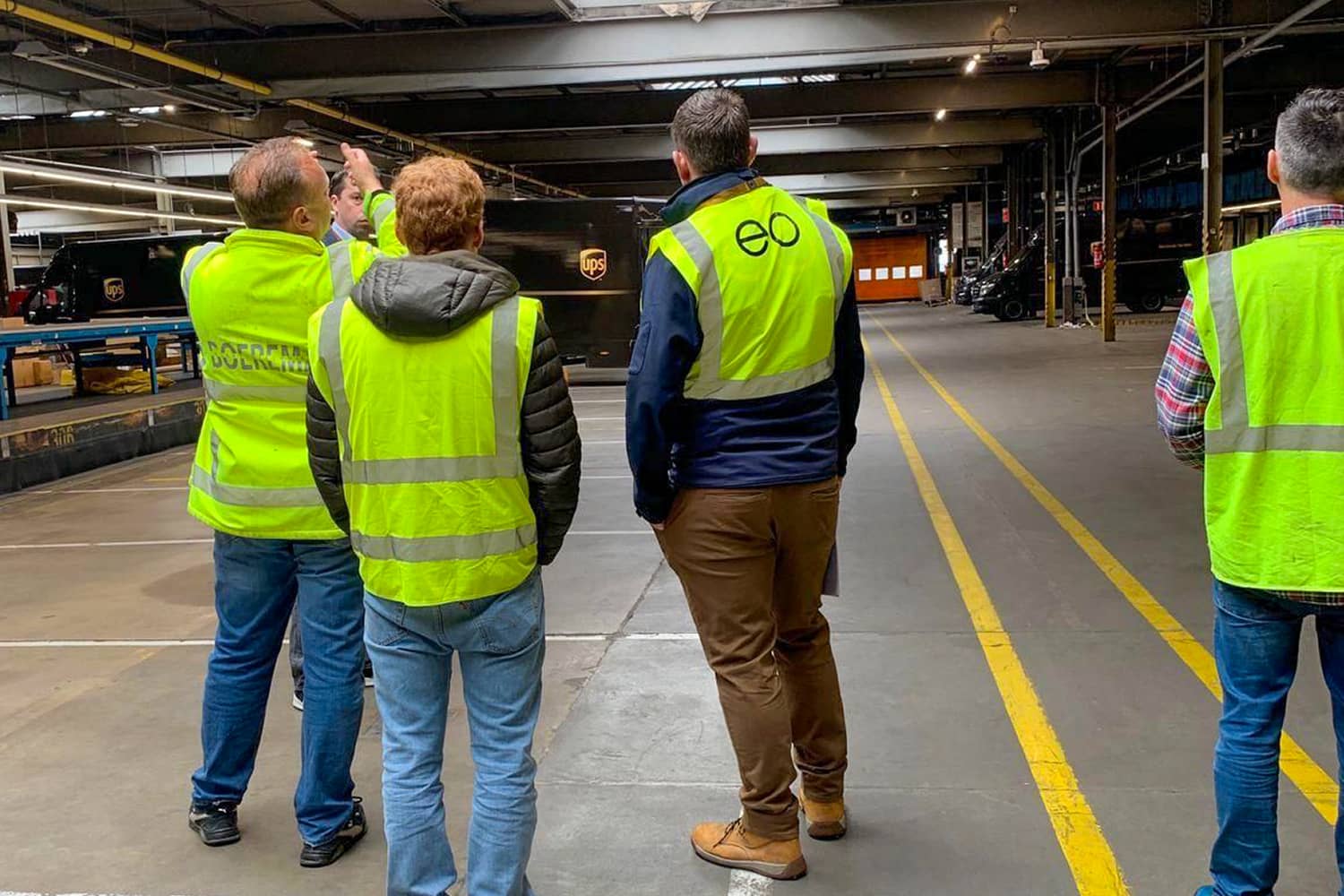
Pre-Construction: Laying the Groundwork for Success
The first step is to ensure full compliance with the Construction, Design, and Management Regulations 2015 (CDM), which are essential for the safe and efficient construction of a depot. Adherence to these regulations is a legal requirement as they prioritise health, safety, and environmental considerations from the start of the construction process. Achieving full compliance requires detailed planning, thorough documentation, and collaboration among all parties involved.
Key elements of the pre-construction phase include:
Collation of Pre-Construction Information (PCI): Pre-construction Information (PCI) is an essential component of construction work and a legal requirement in the planning phase of every construction project in Great Britain. It is a vital step to communicate and understand relevant health and safety information before a project moves into Design and Construction. Critical in helping all stakeholders understand the risks and hazards associated with the project, enabling us to mitigate risk.
Risk Assessments and Method Statements (RAMS): These are crucial for evaluating potential hazards on-site and defining safe working methods. RAMS help mitigate risks by outlining the steps to be taken to avoid incidents and ensure safety for all personnel. EO plays a key role in working with project stakeholders to ensure that all potential risks are identified early on and that safe working practices are established. Our expertise ensures these assessments are comprehensive and meet the specific needs of the depot’s electrification requirements.
Construction Phase Plan (CPP): The CPP is a critical document that outlines key responsibilities, safety measures, timelines, and resource allocation. It serves as a blueprint for how the project will be carried out safely and effectively. At EO, we assist in developing and managing the CPP, ensuring it covers all aspects of the construction phase, from worker safety to equipment and site logistics. By coordinating with contractors and stakeholders, we help to ensure smooth execution in line with the timeline and regulatory requirements.
Health & Safety Schemes and Certifications: Compliance with industry standards is a must. This includes meeting high compliance requirements such as Avetta, Constructionline, and Safe Contractor Alcumus certifications. These certifications demonstrate that the project meets the required safety standards. EO works to ensure that every phase of the project is covered by these safety schemes, liaising with all involved parties to ensure that proper health and safety standards are implemented throughout every step. Our team is dedicated to supporting your project with the necessary documentation and certification consultations, providing peace of mind throughout this process.
By focusing on these critical pre-construction elements, depot projects can adhere to industry safety and quality standards. This establishes a foundation for constructing a reliable infrastructure that supports long-term fleet operations. EO’s involvement guarantees the effective implementation of these essential compliance and safety measures, and we help manage the overall process to meet both regulatory and operational requirements.
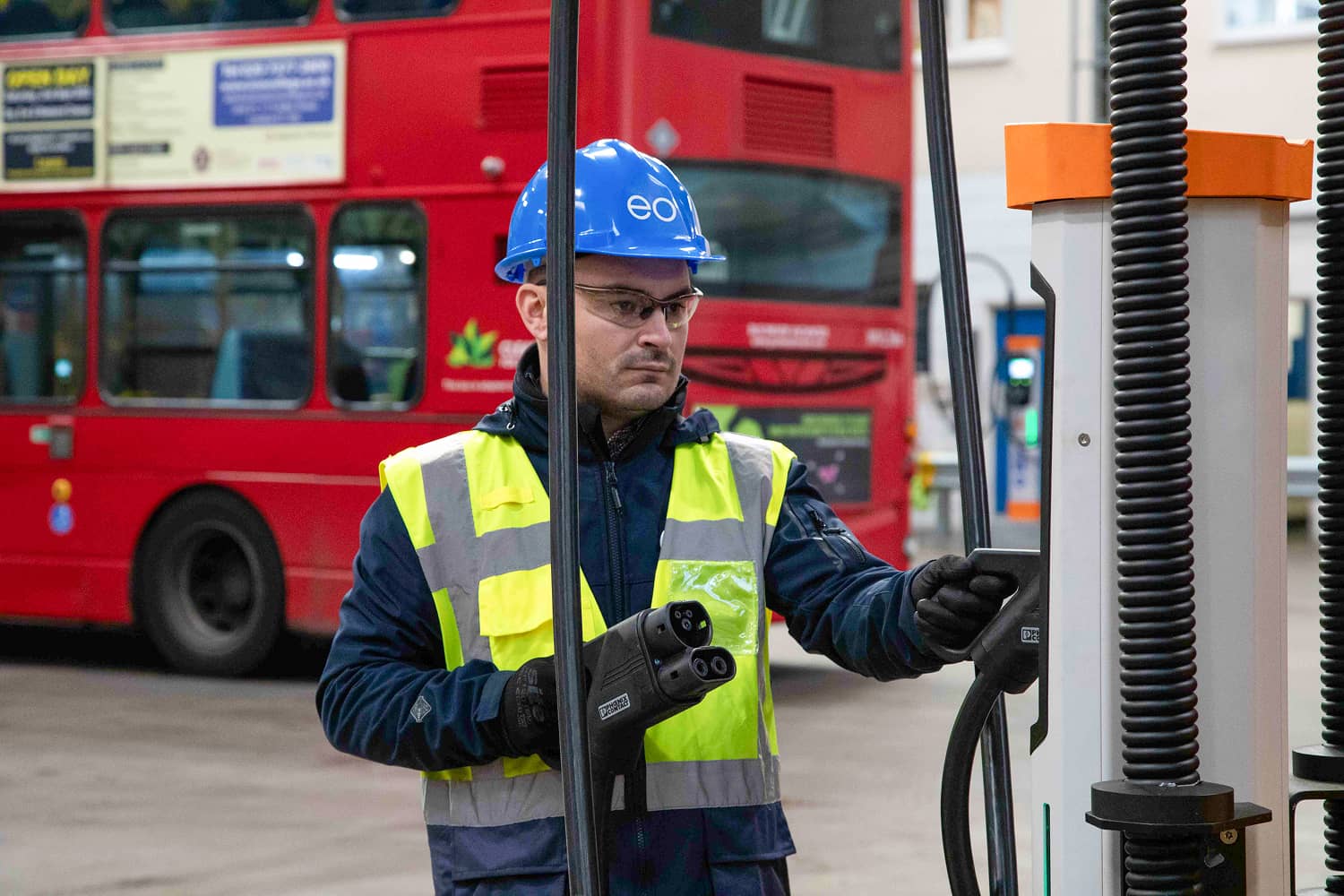
Construction: Bringing Charging Infrastructure to Life
The construction phase is where the planning of your depot is brought to life. This critical stage involves transforming the vision of your electrified fleet into a fully functional, efficient, and future-ready facility. A well-organized approach is essential, and it should encompass the following key aspects:
Comprehensive CDM Management: Ensuring that all legal and safety requirements, identified during the pre-construction phase, are adhered to throughout the build. This includes continued risk assessments and regular monitoring of safety practices to maintain compliance with the Construction, Design, and Management (CDM) Regulations. At EO, we assist in managing ongoing CDM requirements, including overseeing site safety, ensuring that all subcontractors comply with the highest safety standards, and conducting regular site inspections. Our goal is to make sure that safety remains a top priority throughout the construction process, minimising risk and avoiding costly delays.
Infrastructure Installation: This is the physical build of your depot, from groundwork to charger integration. The focus here is on optimising the installation for both efficiency and cost-effectiveness. EO oversees this process by coordinating the installation of electrical infrastructure, ensuring that every aspect is executed according to plan. This includes everything from power supply management to the integration of the charging units. We work closely with stakeholders to ensure all installations are completed in a timely manner, meet industry standards, and are future proofed for scalability.
Preventative Maintenance Coordination: To minimise downtime and maintain the operational reliability of the depot, a proactive maintenance strategy is essential. At EO, we integrate this into every build throughout the feasibility and design process, ensuring a seamless handover when the infrastructure is put into operation. We assist in setting up maintenance schedules that align with the depot's operational needs, ensuring regular checks and maintenance to keep your infrastructure running smoothly. We work with you to implement preventative maintenance procedures and ensure that all equipment is performing optimally to avoid unexpected issues. This strategy helps enhance long-term fleet performance and ensures minimal disruption during operation.
Dedicated Project Management: Clear communication and adherence to timelines are essential to the successful completion of a construction project. EO provides dedicated project management support, overseeing every stage of the build. Our project managers serve as the primary point of contact for all stakeholders, ensuring that construction runs smoothly, funding requirements are met, and timelines are adhered to. We work to address any potential issues quickly, keeping the project on track and making sure that client expectations are met.
By managing each aspect of the construction process efficiently, depot electrification can be implemented in a standardised, cost-effective, and scalable manner. EO’s expertise in coordinating infrastructure, managing safety, and optimising processes ensures that your depot is ready for long-term fleet operations and future expansion.
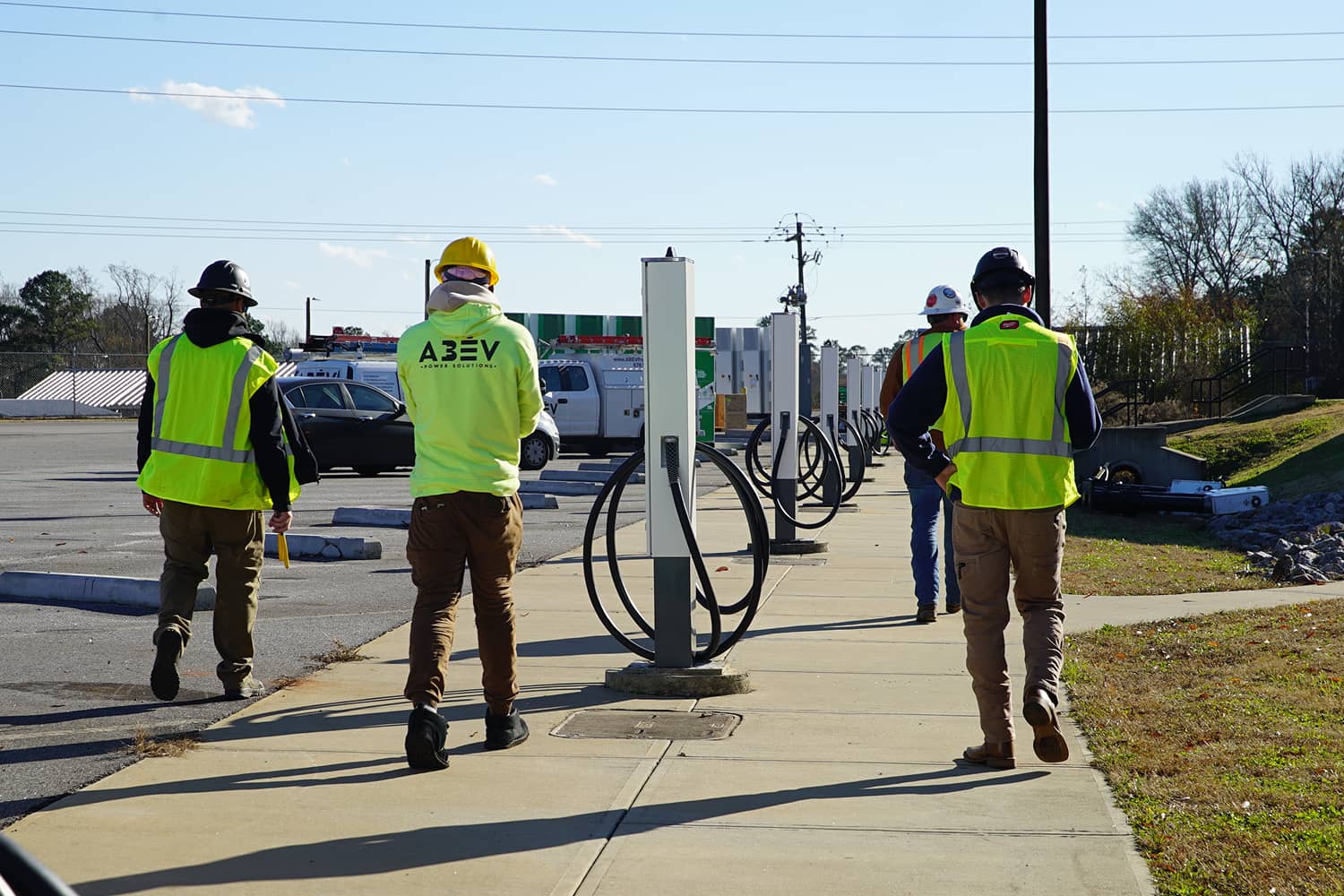
Delivery & Handover: Ensuring Long-Term Success
Upon project completion, a comprehensive commissioning package should be provided to ensure a smooth transition. This package serves as an essential reference for maintaining and operating your depot infrastructure even after the project has been finalised. Key components include:
All Necessary Certification Documents: These documents confirm that the infrastructure complies with all regulatory standards, ensuring that the depot is built to meet industry guidelines for safety, performance, and environmental impact. EO ensures that all certifications are provided promptly and accurately, including testing reports, compliance certificates, and proof of installation. We also assist in any necessary post-handover audits or inspections to guarantee ongoing compliance as your depot evolves.
As-Built Drawings: These detailed drawings document the final layout of the infrastructure, including electrical systems, charging points, and any additional installations made during construction. At EO, we ensure that these drawings are comprehensive, easy to understand, and accurately reflect the installed systems, making them a critical tool for long-term maintenance and operational efficiencies.
A Full Site Walkthrough: A thorough site walkthrough is conducted to help familiarise you with your new charging setup. This includes a detailed explanation of the infrastructure, how to operate the charging stations, and how to maintain the system for optimal performance. EO’s team provides this walkthrough to ensure that all aspects of the depot are fully understood, from the operation of the charging infrastructure to troubleshooting basic issues. This helps ensure that your team can confidently operate and manage the depot correctly.
Beyond the handover, ongoing support and system optimisation are key to ensuring the depot remains reliable, adaptable, and ready to meet the evolving needs of your fleet. EO offers continuous support to help you troubleshoot any operational issues and optimise the charging infrastructure as your fleet grows. Our team is available for regular check-ups and system upgrades, ensuring that your depot is not only performing at its best but also future-proofed for upcoming changes in fleet operations and technology advancements.
Electrifying a depot is a significant investment in the future of fleet operations. A well-executed construction phase minimises risks, maximises efficiency, and ensures long-term success. Proper planning, expert project management, and adherence to industry regulations will result in a seamless transition to electric operations.
At EO, we ensure a smooth and efficient depot electrification process, managing everything from compliance to installation and long-term support. Our expertise in fleet charging infrastructure helps businesses future-proof their operations and optimise their transition to electric vehicles. Visit our Development & Construction page for insights into how we deliver seamless, future-proof infrastructure.